Fasteners and Machining: Enhancing Longevity and Efficiency in Production
Fasteners and Machining: Enhancing Longevity and Efficiency in Production
Blog Article
Grasping the Art of Fasteners and Machining: Developments and Finest Practices
In the realm of industrial manufacturing and engineering, the mastery of fasteners and machining is a foundation of making sure architectural stability, capability, and longevity in various applications. As technology developments and needs for performance and precision increase, remaining abreast of the most up to date innovations and best techniques in fastening and machining ends up being essential. From the advancement of securing modern technologies to the details of choosing the most ideal materials, the landscape of modern production is constantly evolving. Join us as we check out the most up to date advancements and look into the nuanced globe of grasping fasteners and machining, revealing crucial insights and methods that can elevate your strategy to engineering remedies.
Development of Attachment Technologies
Throughout the commercial revolution and into the modern-day era, the development of attaching technologies has been marked by continuous advancements in effectiveness and integrity. Bolts, such as screws, screws, and rivets, play a vital duty in different markets, consisting of auto, aerospace, building and construction, and electronics. The requirement for stronger, a lot more sturdy, and easier-to-install fastening services has actually driven technology in the field.
One significant advancement has been the change towards precision machining strategies to create fasteners with greater resistances and superior performance. This change has actually made it possible for suppliers to produce fasteners that satisfy stringent high quality standards and offer raised resistance to deterioration and fatigue.
Additionally, the intro of advanced products, such as titanium alloys and composites, has changed the abilities of bolts. Fasteners and Machining. These materials offer outstanding strength-to-weight proportions, making them excellent for applications where reducing weight is essential without jeopardizing architectural stability
Developments in Machining Methods
In the realm of industrial production, the constant evolution of machining techniques has led the means for unmatched accuracy and effectiveness in the manufacturing of fasteners. This exact control enables makers to create complicated and intricate fastener layouts with ease.
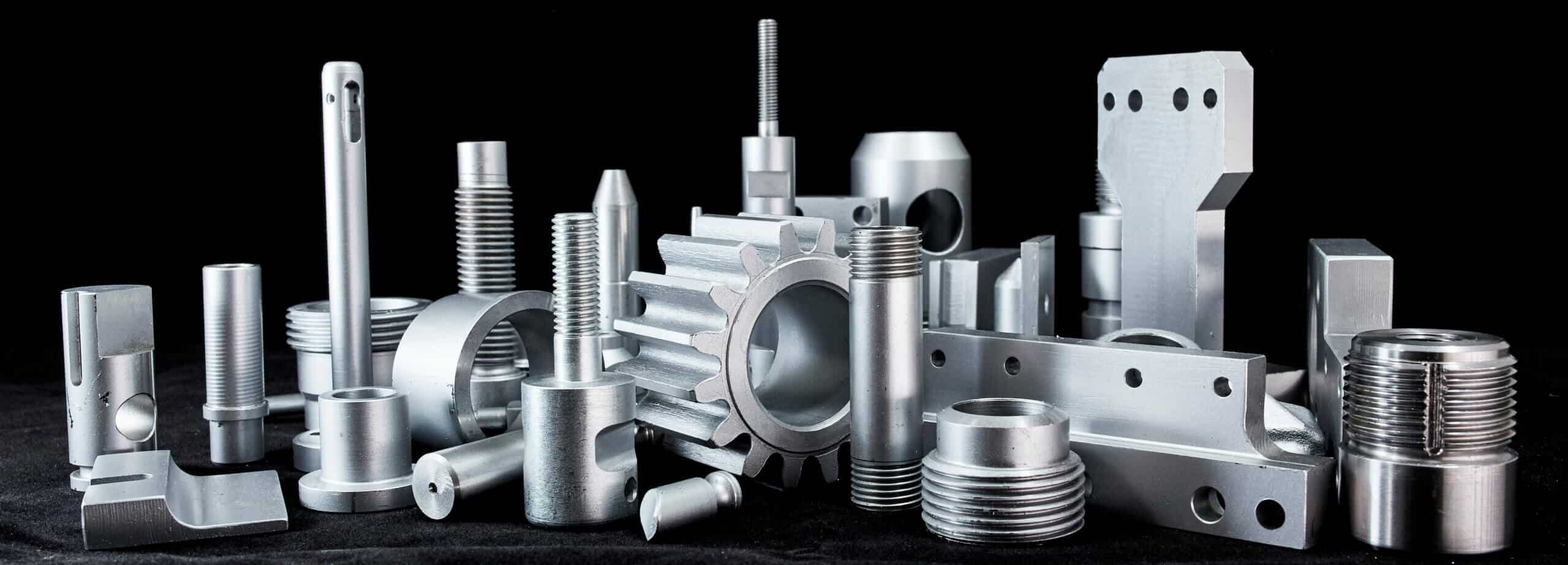
Furthermore, the adoption of multi-axis machining facilities has actually enabled synchronised cutting procedures from numerous angles, even more enhancing performance and minimizing production times. By making use of these sophisticated machining methods, suppliers can satisfy the enhancing need for top notch fasteners while keeping cost-effectiveness in their operations.
Choosing the Right Bolt Materials
Choosing the appropriate product for fasteners is an essential decision that considerably influences the performance and durability of the set up components. When picking straight from the source the best bolt material, a number of factors need to be considered to make sure the resilience and integrity of the final item. The product chosen need to be compatible with the ecological problems the fasteners will be revealed to, such as temperature level variants, dampness levels, and harsh elements.
Typical products used for fasteners include stainless steel, carbon aluminum, titanium, and steel, each offering one-of-a-kind buildings that suit different applications. Stainless steel, as an example, is known for its corrosion resistance, making it suitable for marine or outside atmospheres. Carbon steel is a cost-efficient option suitable for several general-purpose applications. Light weight aluminum is lightweight and frequently utilized in markets where weight is an important variable. Titanium, on the various other hand, is exceptionally strong and corrosion-resistant, making it appropriate for high-performance applications.
Enhancing Accuracy in Machining
Accomplishing optimal precision in machining is essential for making sure the quality and efficiency of machined elements. Accuracy in machining refers to the capability to consistently create components within tight resistances and with high precision. To improve accuracy in machining, manufacturers utilize a selection of advanced methods and technologies. One secret approach is utilizing Computer Numerical Control (CNC) equipments, which provide premium accuracy and repeatability contrasted to standard hand-operated machining methods. CNC makers are programmable and can implement complex machining operations with very little human treatment, causing higher precision degrees.
Along with here are the findings CNC machining, the use of innovative cutting tools and device owners can likewise significantly improve precision. Premium cutting tools with innovative finishes lower rubbing and wear, leading to more accurate cuts and dimensional precision. Implementing rigid high quality control procedures throughout the machining process, such as regular evaluations and calibration of tools, helps keep regular accuracy levels. By prioritizing accuracy in machining, suppliers can attain remarkable product quality, tighter tolerances, and enhanced total efficiency of machined components.
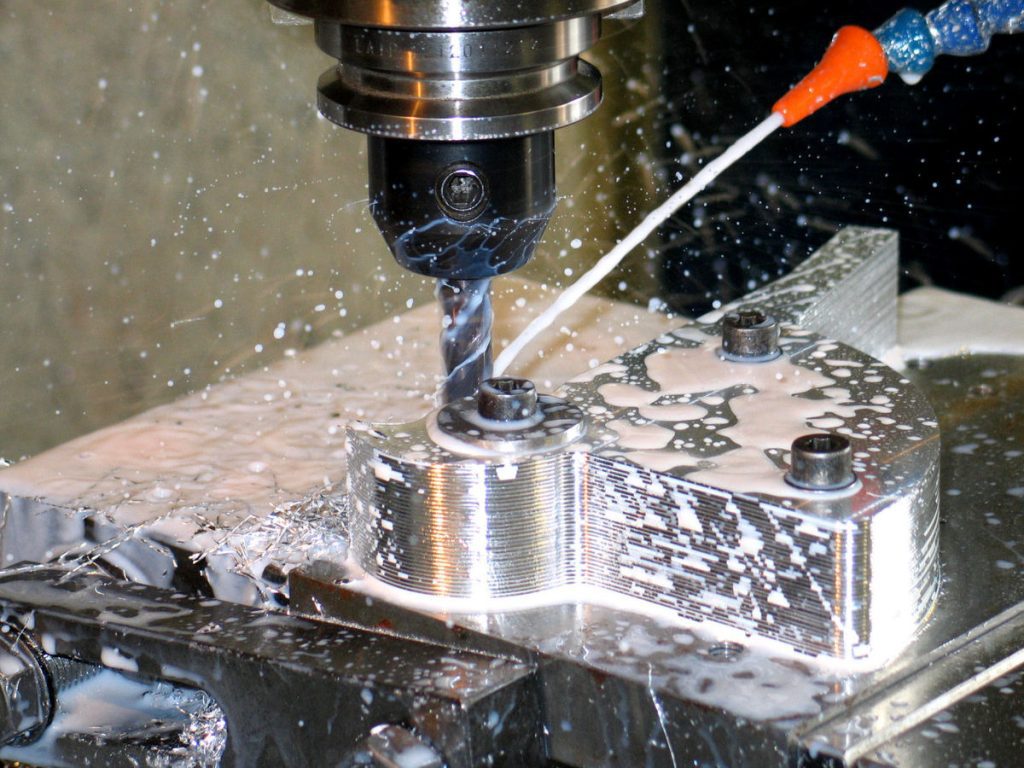
Best Practices for Bolt Installment
Precision in machining plays an important role in ensuring the integrity and durability of fastener installments. When it comes to finest methods for fastener installation, one key element is the correct selection of bolts based on the particular application requirements.
In addition, making sure that the fastener strings are totally free and tidy of debris prior to setup is vital to attaining a protected and reliable connection. Making use of thread-locking compounds or washing machines can also improve the security of the fastener setting up. Regular assessments and maintenance of fasteners post-installation are advised to identify any kind of potential problems at an early stage and protect against costly fixings or replacements in the future. By adhering to these ideal practices, suppliers can enhance the honesty and performance of their bolt installations.
Final Thought
By selecting the ideal fastener products and enhancing accuracy in machining, makers can attain ideal results in their operations. On the whole, understanding the art of fasteners and machining involves continual development and adherence to finest practices.
In the realm of commercial manufacturing, the continuous development of machining methods has actually paved the means for extraordinary precision and performance in the manufacturing of fasteners.Accuracy in machining plays a crucial duty in making sure the dependability and longevity of bolt installations. When it comes to ideal methods for fastener our website setup, one key facet is the appropriate option of bolts based on the specific application needs. By choosing the appropriate fastener products and improving accuracy in machining, makers can achieve ideal results in their procedures. Overall, mastering the art of bolts and machining involves continual development and adherence to ideal practices.
Report this page